Існуе мноства тыпаў пластыкавых лістоў з шырокім спектрам выкарыстання.У цяперашні час асноўнымі відамі з'яўляюцца полівінілхларыду, полістырол і поліэстэр (ПЭТ).Ліст ПЭТ мае добрыя характарыстыкі і адпавядае нацыянальным патрабаванням індэкса гігіены для фармованых вырабаў і міжнародным патрабаванням аховы навакольнага асяроддзя.Яны належаць да табліцы аховы навакольнага асяроддзя.У цяперашні час упакоўка павінна адпавядаць патрабаванням аховы навакольнага асяроддзя і перапрацоўкі, таму попыт на ПЭТ-лісты становіцца ўсё больш і больш.У гэтым артыкуле ў асноўным абмяркоўваецца працэс вытворчасці і агульныя праблемы лістоў ПЭТ.
Тэхналогія вытворчасці лістоў ПЭТ:
(1) ліст ПЭТ
Як і іншых пластмас, уласцівасці ПЭТ ліста цесна звязаны з малекулярнай масай.Малекулярная маса вызначаецца характарыстычнай глейкасцю.Чым вышэй характарыстычная глейкасць, тым лепш фізічныя і хімічныя ўласцівасці, але дрэнная цякучасць і складанасці ў фарміраванні.Чым ніжэй характарыстычная глейкасць, тым горш фізічныя і хімічныя ўласцівасці і ўдарная трываласць.Такім чынам, унутраная глейкасць ліста ПЭТ павінна быць 0,8 дл/г-0,9 дл/г.
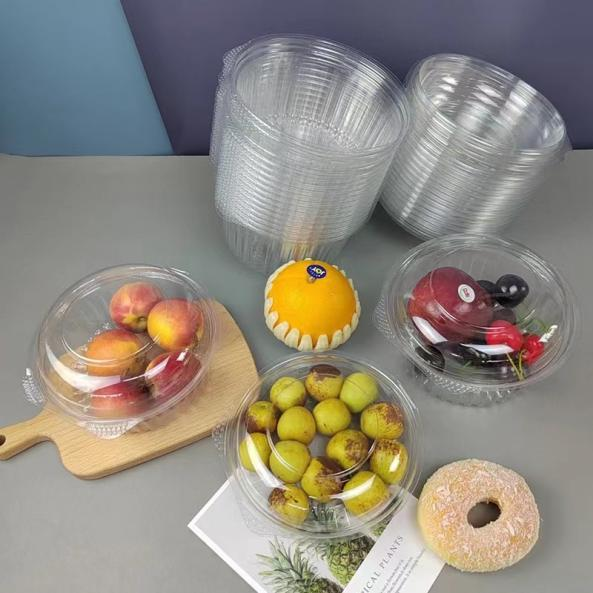
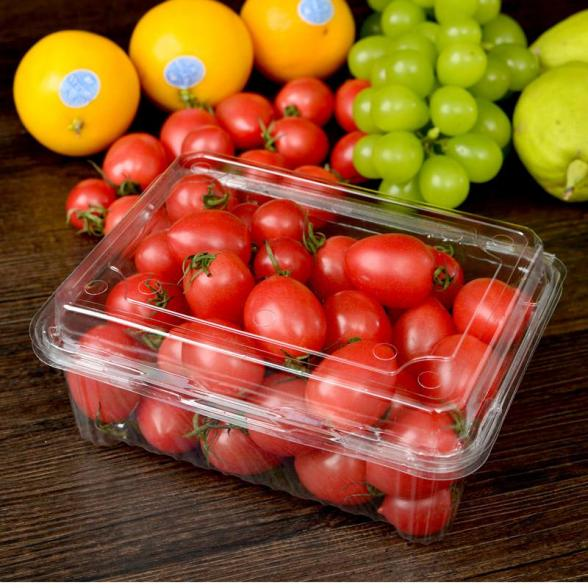
(2) Паток вытворчага працэсу
Асноўныабсталяванне для вытворчасці лістоў ПЭТуключае крышталізацыйныя вежы, сушыльныя вежы, экструдары, галоўкі, трохвалковыя каландры і намоткі.Працэс вытворчасці: крышталізацыя сыравіны-сушка-экструзія-пластыфікацыя-экструзія-ліццё-каландраванне і фармоўка-намотка вырабаў.
1. Крышталізацыя.Лустачкі ПЭТ награваюць і крышталізуюць у крышталізацыйнай вежы, каб выраўнаваць малекулы, а затым павялічваюць тэмпературу шклянога пераходу лустачак, каб прадухіліць адгезію і засмечванне бункера ў працэсе сушкі.Крышталізацыя часта з'яўляецца важным этапам.Крышталізацыя займае 30-90 хвілін, а тэмпература ніжэй за 149°C.
2.Сухі.Пры высокіх тэмпературах вада будзе гідралізаваць і разбураць ПЭТ, што прывядзе да памяншэння яго характэрнай адгезіі, а яго фізічныя ўласцівасці, асабліва ўдарная трываласць, будуць зніжацца па меры памяншэння малекулярнай масы.Такім чынам, перад плаўленнем і экструзіяй ПЭТ трэба высушыць, каб паменшыць утрыманне вільгаці, якое павінна быць менш за 0,005%.Для сушкі выкарыстоўваецца асушальная сушылка.З-за гіграскапічнасці ПЭТ-матэрыялу, калі вада пранікае глыбока ў паверхню зрэзу, будуць утварацца малекулярныя сувязі, і іншая частка вады будзе пранікаць глыбока ў зрэз, што ўскладняе сушку.Таму звычайны гарачы паветра выкарыстоўваць нельга.Кропка расы гарачага паветра павінна быць ніжэй за -40C, і гарачае паветра паступае ў сушыльны бункер праз замкнёны контур для бесперапыннай сушкі.
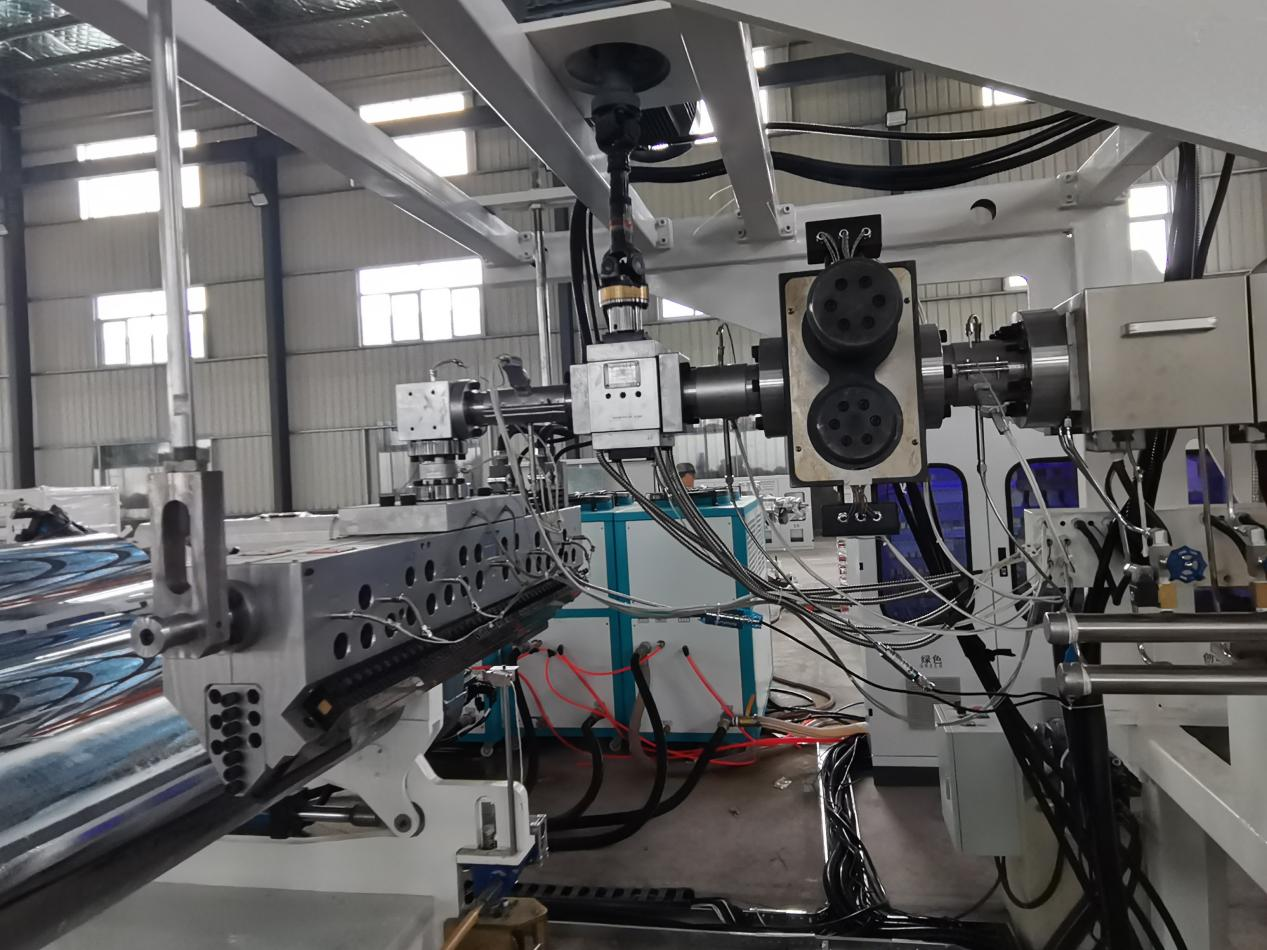
3. Сціскаць.Пасля крышталізацыі і сушкі ПЭТ ператвараецца ў палімер з відавочнай тэмпературай плаўлення.Тэмпература фармавання палімера высокая, а дыяпазон рэгулявання тэмпературы вузкі.Для аддзялення нерасплаўленых часціц ад расплаву выкарыстоўваецца спецыяльны бар'ерны шнек для поліэстэру, які дапамагае падтрымліваць больш працяглы працэс зруху і павялічвае прадукцыйнасць экструдара.Прымае гнуткую плашку з абцякальнай дросельнай засланкай.Галоўка формы звужаная.Абцякальныя бегуны і вусны без драпін паказваюць, што аздабленне павінна быць добрым.Награвальнік формы мае функцыі дрэнажу і ачысткі.
4.Астуджэнне і фарміраванне.Пасля таго, як расплаў выходзіць з галоўкі, ён непасрэдна трапляе ў трохвалковы каландр для каландравання і астуджэння.Адлегласць паміж трохвалковым каландрам і галоўкай машыны звычайна захоўваецца на ўзроўні каля 8 см, таму што, калі адлегласць занадта вялікая, дошка лёгка правісне і зморшчыцца, што прывядзе да дрэннай аздаблення.Акрамя таго, з-за вялікай адлегласці рассейванне цяпла і астуджэнне адбываюцца павольна, і крышталь становіцца белым, што не спрыяе качэнню.Трехвалковый каландровый блок складаецца з верхняга, сярэдняга і ніжняга валкоў.Вал сярэдняга роліка замацаваны.У працэсе астуджэння і каландравання тэмпература паверхні роліка складае 40°C-50C.Вал верхняга і ніжняга ролікаў можа рухацца ўверх і ўніз.
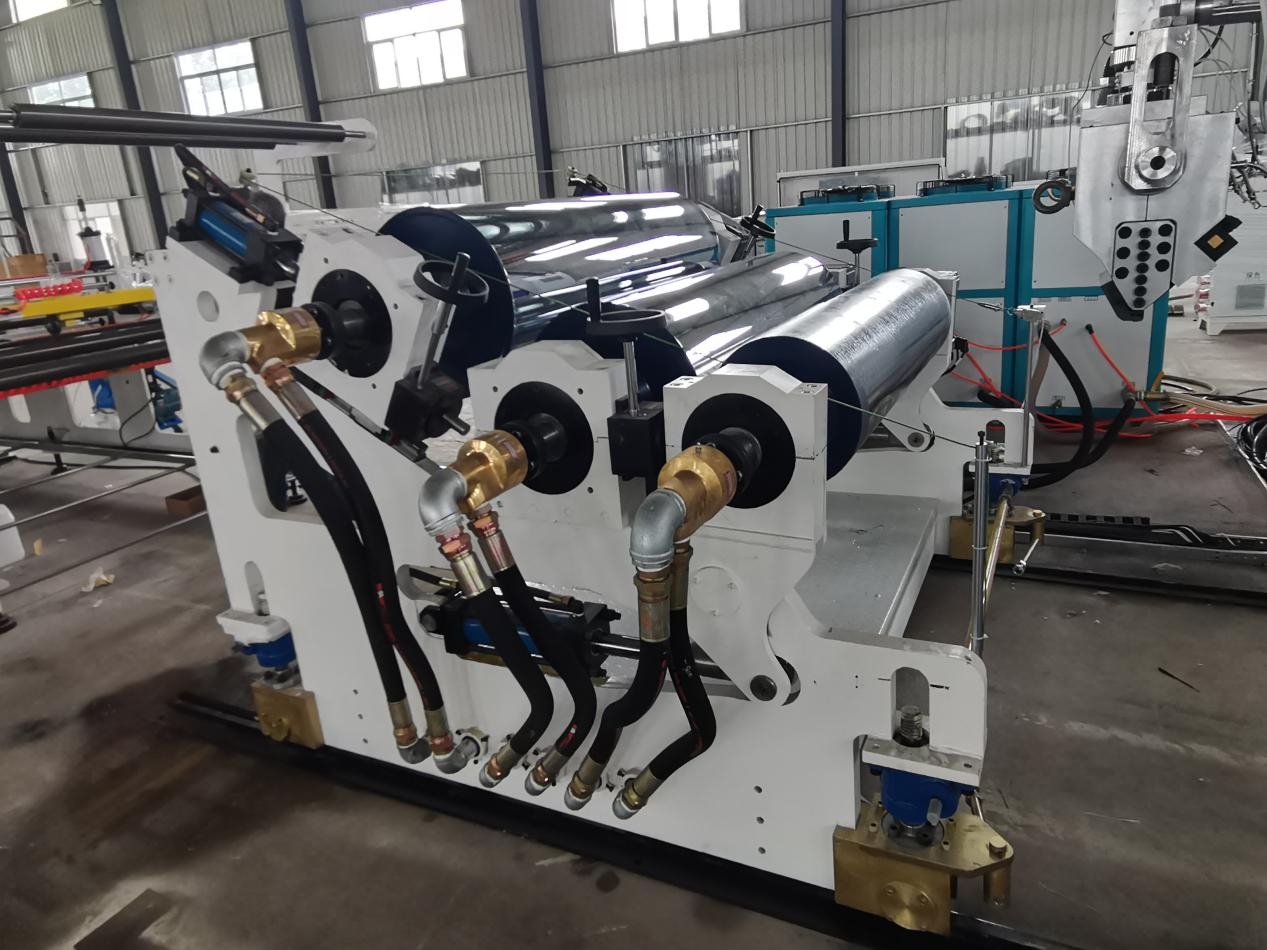
Час публікацыі: 28 верасня 2023 г